Welding powder for producing E6013
Applications:
E6013 welding powder for making welding electrode, which is a kind of carbon steel electrode with iron powder titania type coating. AC/DC. All-position welding. It has excellent welding performance and is almost spatter-free. It has easy re-ignition, good slag detachability, smooth welding appearance. Common grade and rutile grade for you to choose.
Features:
1.Quick strike & Easy restrike & Easy slag-removal
2.Stable arc performance & minimal arc interference
3.Smooth and shiny appearance & Excellent mechanical properties
4. High efficiency and high impact values at -30c.
5. High deposition rates
6. Excellent crack resistance and x-ray performance
7. Packing: 300kgs damproof bag packaging; or as you required
Attention:
1.Electrode must be approved by 350-380℃ for 1 hour before welding, dry the electrode when use it.
2. The rust, oil, water and other impurities of the weld must be removed before welding.
3.You must use short arc welding,the swings should not be too large, narrow bead welding is appropriate.
4. To prevent producing arc porosity, arc plate should be adopted or use return method for arc welding.
Chemical Composition:
Elements | TiO2 | AL2O3 | SiO2 | Mn | CaO+MgO | Organic | Other |
Actual result | 42 | 4.5 | 28 | 9 | 10.5 | 4 | 2 |
Welding electorde powder of E7018, E6011, E6010, E7024, etc are also available. Pls contact us for more details.
Process technical requirements:
Important welding parts should be clearly marked in accordance with relevant regulations when preparing welding procedure specifications.
Assembling the mold (assembly fixture) of the welded parts, the amount of welding shrinkage must be considered. It should be ensured that the tolerances of the welded parts are within the design requirements.
Before assembling, remove the rust, oil, dust and moisture within no less than 25mm on both sides of the weld. For important welds of low-alloy structural steel, oxide scale should be removed.
The assembly gap should be controlled during assembly. The gap of butt welds is 2~3mm, and the gap of fillet welds is 0~2mm. When the local gap is too large, try to trim it to the specified size. It is strictly forbidden to add fillers in the gap, and strong pairing is prohibited to reduce the residual stress in the welded components.
The welding materials and process parameters used in the assembly tack welding shall be the same as the formal weld requirements.
Welding operations can only be carried out after the welding parts have passed the assembly inspection.
For new materials and new processes, process tests must be done and they can be used only after they are qualified.
The welding slag and defects at the root of the weld must be removed before welding the reverse weld of the weld and other grooved welds
Welding can only be performed after cleaning.
Before welding, it is forbidden to start arc ignition and test current adjustment in the non-welding area. After welding, the surface of the weld should be cleaned and dried.
Net, for important welding parts of important welding parts, the welder’s mark should be marked in the appropriate position after welding.
For steel plates with a thickness of 0.3~4mm, welding methods such as gas metal arc welding or argon tungsten arc welding are mainly used.
For the welding of dissimilar steel components, electrodes, wires and fluxes of the same strength grade should be selected.
When welding low-alloy structural steel, it is not advisable to stop in the middle, and try to complete the welding at one time; during multi-layer welding, the joints between layers should be staggered and the temperature between layers should be controlled between 250~300℃. Before welding the next layer of welding seam, it should be cleaned. Check the weld of the upper layer to ensure that there are no defects.
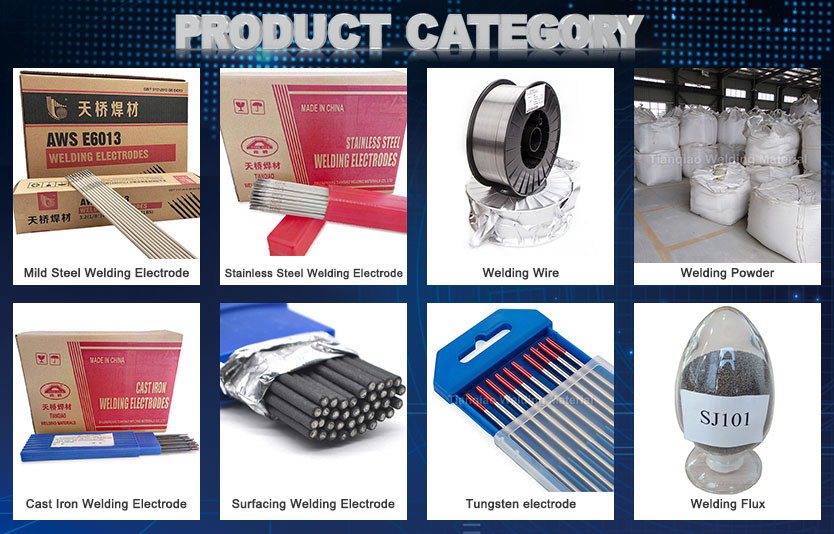